Sergio Visini comes from Franciacorta, a district in the province of Brescia in the Italian region of Lombardy. This area is known for the production of "Franciacorta wine". Coming from a crop farming family (he never had any contact with the pig world) , he studied economics and commerce and wanted to reproduce the formula that has been promoting the Franciacorta wine. Thus Piggly was born, a company that owns 850 sows in the Veneto region and 11,000 animals in nursery-finishing in the municipality of Pegognaga (Lombardia region). The sow farm, which is not the subject of this report, has been almost completely restructured and the nursery and finishing facilities are new, with an uncommon, highly aesthetic design.
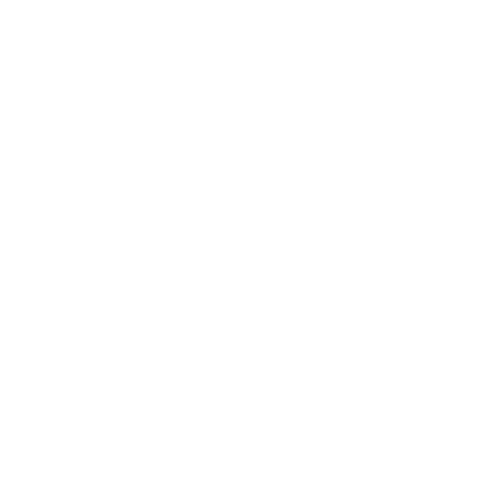
We have to begin immediately by specifying that the farm has practically "zero carbon footprint", and this is exactly where the project started in 2012: first the photovoltaic panels were built (2 megawatts) and then the buildings... just underneath! and the biogas (637 kW). The initial investment served to finance the successive constructions, starting with the finishing barns and ending in 2017 with the three weaning barns that work using straw. Moreover, the farm is "antibiotic-free from birth": the treated pigs are identified with ear tags and represent about 2% of the production. Let's get into the questions:
From an environmental point of view, how have you managed to significantly reduce your carbon footprint?
Easy:
- We use very little electricity at the barns, there is no forced ventilation or other equipment that consumes a lot of energy. In the end, only 10% is used on the farm, the rest goes to the grid.
- Biogas accounts for more than 70% of the reduction in emissions; only the thermal energy goes to the farm, and the rest goes to the grid. In addition, the digestate produced is used on our land; we do not buy chemical fertilizers.
Sergio, what is weaning on straw like? This is a topic that "scares" many farmers.
First of all, I would like to say that I was initially very hesitant about straw and an all-natural ventilation system in this delicate phase of the piglets. I went for my objectives: to make a quality product that is environmentally friendly, low in energy costs, and very committed to animal welfare, which could positively impress even the most demanding consumer. Technically, the straw must be cut with a maximum length of 10 cm and an average daily quantity of 200 g per head, from start to finish.
For cleaning, we have built an easy-to-manage environment in which the piglets can be completely confined so that cleaning can be done once a week for the first 2-3 weeks and twice a week when they are larger (they can reach up to 40 kg at this stage). Two people and a payloader are needed for the cleaning procedures, which take about one hour each time. Having such a high health status allows us to spend much less time on treatments. At this stage, the average daily gain is about 600 g/animal/day. The cost of straw and labor is 2.5 euros/head.
An important detail is the temperature: at the beginning, we were "afraid" of the cold, but today, after several experiments, we have been able to stay at 20°C in winter (there is a heat radiator that uses the thermal energy of the biogas). With the straw, there is no need for higher temperatures, in addition to benefiting from a more substantial air exchange, we have a height of 6 meters in the highest area (photos 1 and 2).
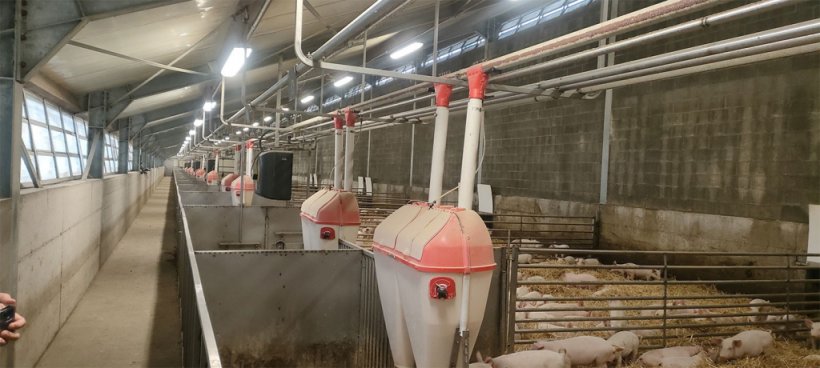
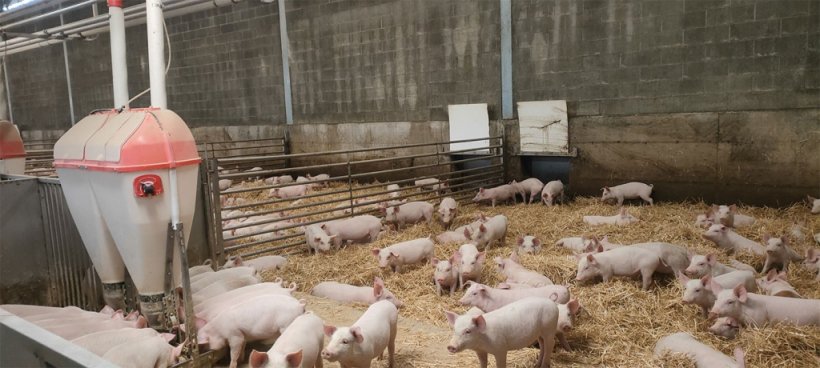
When you visit the farm, it doesn't look like there are pigs inside... How did you do it?
I turned to an architect who does not specialize in the livestock world, who suggested the use of very durable and aesthetically pleasing materials. The outside area is enclosed, both to contain the heat and to give a visual impression of cleanliness. In addition, between the barns we have grass, which helps lower the indoor temperatures during the summer. An outside worker is in charge of maintenance. Regarding the noise level, the pigs are so quiet that we don't hear anything from the outside... only when the finishing pigs receive their feed!! (photos 3,4,5). Tail biting problems are practically non-existent.
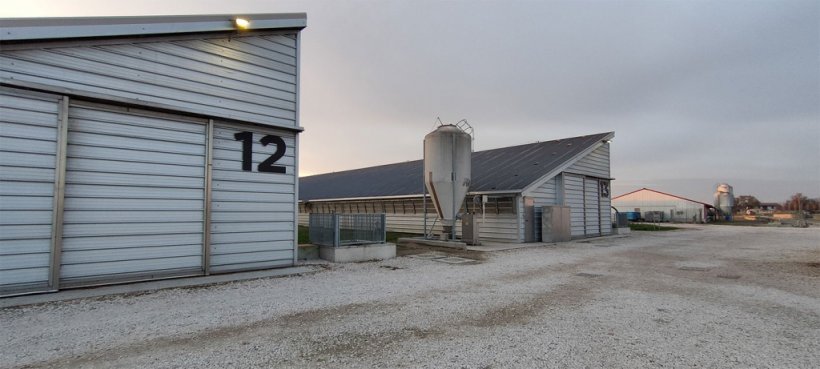

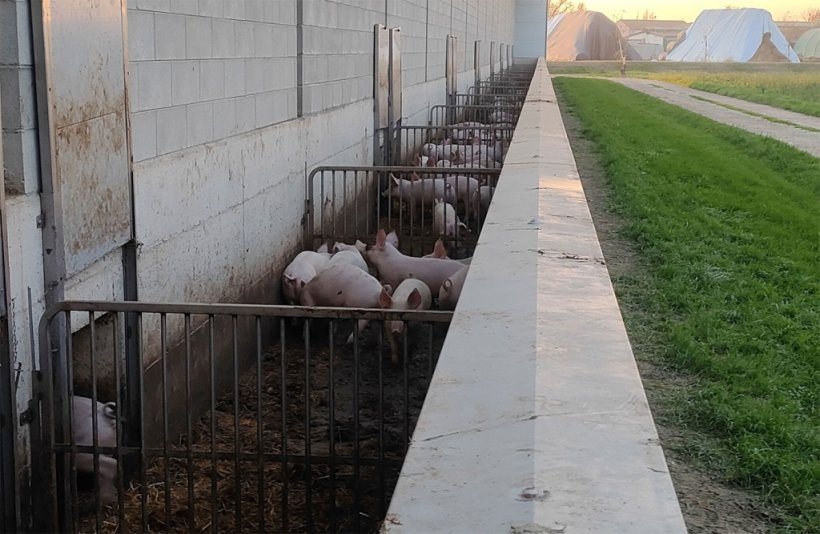
What are the finishing barns like? Does the straw not clog the pits?
Inside they are very normal; logically we provide more space (1.25 m²/head) and we constantly have straw in each pen, offered via a straw dispenser (photos 6 and 7). All the barns (including those for the small piglets) have a single sloped roof and a maximum height of 6 meters, which greatly improves ventilation and means that the pigs do not get dirty to cool themselves in the summer. The solid floor is highly insulated on the inside and slatted on the outside, which serves as a defecation area. The south wall is also very well insulated (all barns are oriented east-west).
We periodically use a set of bacteria of the Bacillus family by atomization to reduce odors and ammonia. It is sprayed directly on the animals, feces, and floor of all the pens, and helps greatly in keeping away insects and flies in general, thus avoiding the use of insecticides.
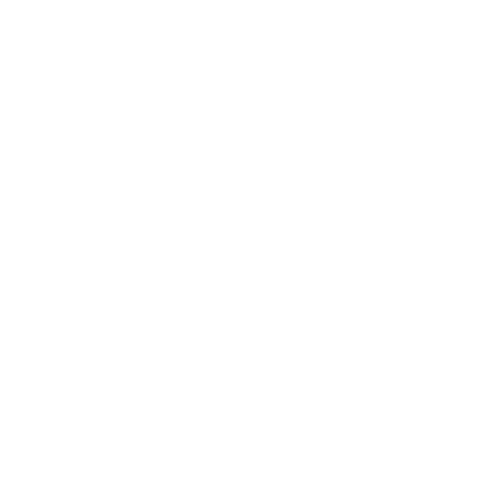
The regular and weekly emptying of the pits located under the outdoor areas by means of a suction system and pipes with adequate diameters, prevents any kind of clogging problems due to the straw, and also reduces the ammonia levels. The weekly frequency prevents compaction.
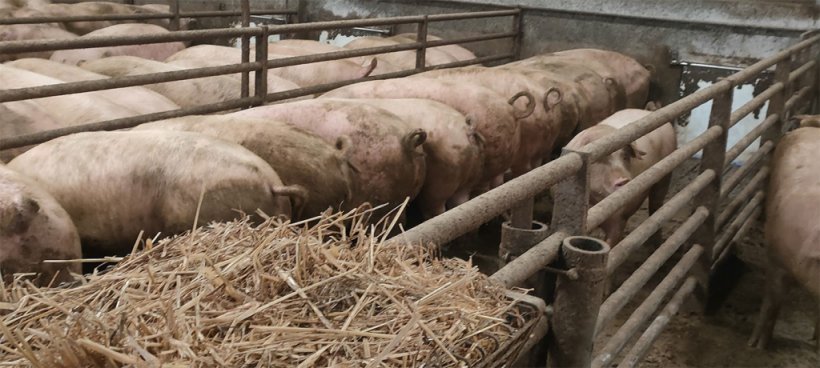
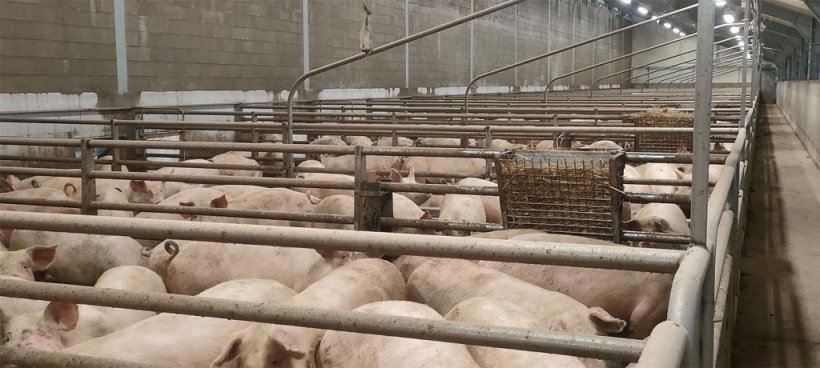
Do you use any special technology? How have you managed to reduce your emissions so much?
Honestly no, we just have ammonia, CO2, temperature, and humidity sensors in all the barns that are constantly monitored in real time (photo 8). The finishing feed is liquid and the piglets are fed dry feed ad libitum. Obviously, the photovoltaic and biogas systems are always connected so that all aspects of energy production are always under control... In the end, we only "emit" 1.06 kg CO2/kg live weight compared to an average of 5.50 kg CO2/kg live weight produced on conventional farms.
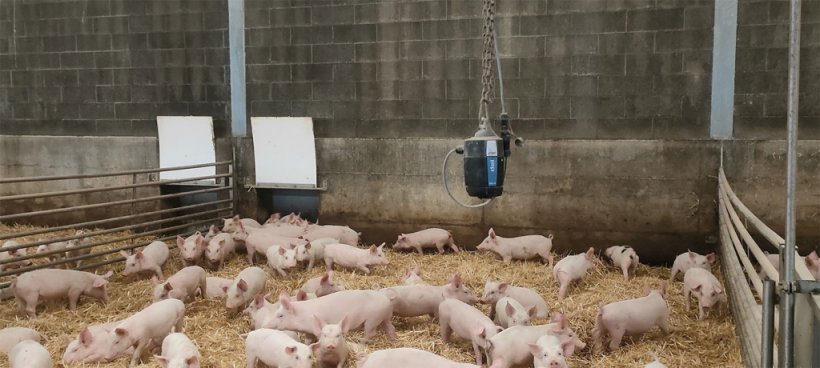
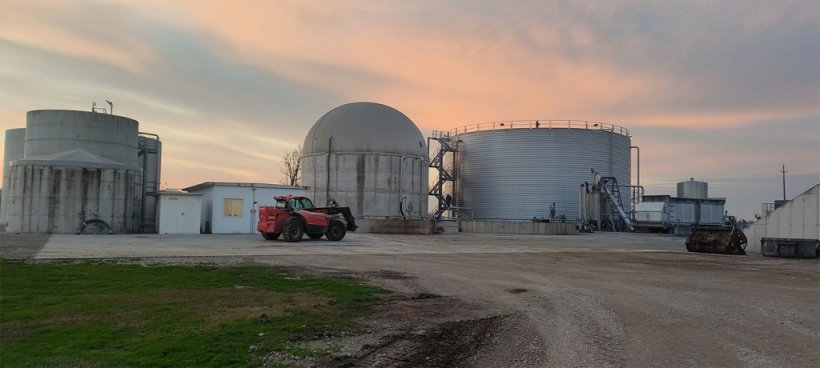
To conclude, does it pay off ?
I would say yes: with an initial investment of 30% more than a traditional system and with proper market recognition and premiums paid for this type of pigs.