Since feeding represents about 60% of all production costs, the increasingly competitive context in pig production makes it essential to optimize all dietary factors that ultimately contribute to improve them.
Research usually focuses primarily on the effect of nutrients and the use of raw materials, paying less attention to the physical characteristics of feed, such as particle size —influenced by the type of grinding—, diameter, pellet length and hardness, and the percentage of fines in the feed.
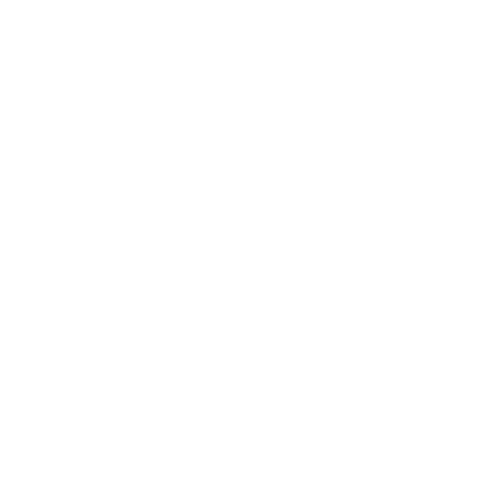
However, there is sufficient information showing that these factors are important. They have been shown to affect feed consumption, as well as digestibility and microbiota of the intestinal tract. The effect is positive in some cases, and negative in others.
There appears to be interactions with the age of the animal, the raw materials used, or the type of feeder, and maybe even genetics.
Practical conclusions that can be implemented in our factories
Particle size will affect the digestibility of nutrients and, therefore, feed conversion. The smaller the diameter, the greater the surface area available to the digestive enzymes, and therefore the greater the digestibility. Particularly important for protein raw materials. Several authors have shown improvements in digestibility of amino acids by reducing the particle size of protein raw materials such as soybean meal, sunflower or rapeseed meal. They have also shown improvements in energy digestibility.
As for grain milling, some studies also support the digestibility and technical results improvements obtained with the use of fine grinds against coarser ones, recommending an average size of about 600-700 μm. This can apply to maize and barley, and especially sorghum. As for wheat, care must be taken if high levels of inclusion are used, since a very fine grind could make the feed pasty, and reduce voluntary consumption.
The difference in the conversion rate expected within a practical range of average particle sizes (D50) between 600 and 1000 microns (between 0.6 and 1.0 mm) can be, possibly, of up to 2-4% between both ends.
A recent Australian work (AC. Edwards, 2014), concluded that a particle size reduction from 1100 to 600 micrometers has no effect on ADG, but reduces consumption, resulting in a FCR improvement of 2.6% in the growth phase, and 5.6% in the finishing phase.
Moreover, it is well known that it's not advisable to use fine grinds (< 500 μm) because of the greater incidence of gastric ulcers, especially in piglets and sows.
Therefore it seems convenient, in pig feed, to use average sizes between 600 and 700 μm.
Consequently, it is important to determine and modify the grinding parameters to improve digestibility and, at the same time, the finer the grind, the better the pellet quality. It is, of course, important to avoid major mistakes, like not grinding soybean supplied as flour, thinking its degree of grinding is good enough. Figure 1 illustrates the particle size distribution curve of an excessively coarse soybean meal.
Figure 1. Soybean meal 47
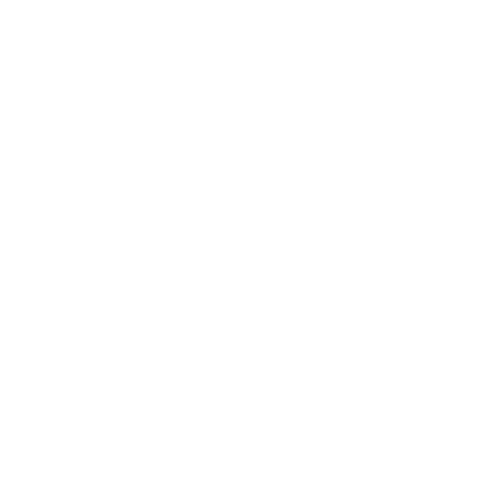
Another major mistake would also be to supply average feed particle sizes above 1300 μm.
How can we measure particle size and uniformity?
It seems simple, but it is usually done incorrectly. A full set of sieves is required, tailored to the sample particle size distribution. Using too few sieves is a common mistake, or when a majority fraction is retained in one of the sieves. In this case we can not accurately determine the average diameter (D50) or the distribution. A minimum of 10 sieves must be used. The cumulative percentage is calculated based on the total weight of the sample and the weight retained on each sieve; then, a particle size distribution curve is drawn using a logarithmic scale. The curve displays the average particle size (D50) —which is the "x" value corresponding to the cumulative fraction of 50%—, and the distribution uniformity.
Sieve stack on a sieve shaker.
The effect of particle size uniformity on the technical results is difficult to assess. Research studies generally use a more uniform grind model, such as the one obtained with a roller mill —as opposed to a hammer mill, which produces more heterogeneous grinds. But when comparing, confusion arises between other possible factors, such as particles sphericity, or homogeneity of nutrients in feed, making it difficult to draw conclusions about the importance of uniformity in the size of the particles, the results being also quite contradictory.
In practice, we might have feeds with a suitable average particle size, but with an excessive coarse fraction (e.g.> 40% bigger than 1000 μm), which digestibility may be lower. In such cases it is advisable to check the grind.
Conclusion
In short, we can conclude that there is insufficient information to prove the importance of particle size, and that both management of grinding parameters to achieve the optimum particle size and monitoring of this parameter in the factory routine quality control checks, will contribute to improve feed conversion rate.