Farmers and companies involved with food production that want a self-sufficient source of electricity and heat could find a combined heat and power (CHP) plant a particularly rational form of energy production. Thanks to recent advances in drive technology and exhaust after-treatment, CHPs can provide the energy needed for farm operations or food production, while meeting future emission limits. The latest engines and exhaust catalyst systems for CHP plants will feature at the EnergyDecentral exhibition, the international trade fair for innovative energy supply, which takes place alongside the EuroTier exhibition from 13 to 16 November 2018 at Hanover.
CHP plants are regarded as the backbone of the German energy network, not least because they result in attractive energy-savings for farmers, who can generate their own electricity from biogas to reduce energy and heating costs. Today's CHP systems can supply most, or not all, of a business’ energy requirements in agricultural or food-producing operations. In addition to supplying electricity, heat recovered from the engine powering the generator can be used in food production processes, or to help heat the farrowing pens in a pig unit. By installing an absorption chiller, surplus heat from a CHP plant can even be converted into cold, by harnessing the evaporation principle, that can be used for cooling milk.
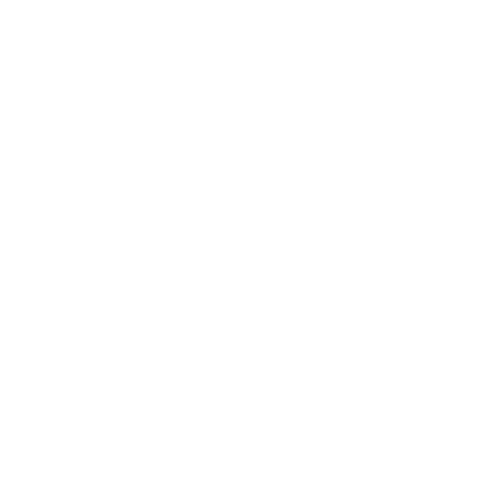
Power plant on the farm
All the key CHP technologies will be presented at EnergyDecentral in Hanover. The exhibitor program includes high-performance systems for the production of electricity, heat and cold, which farmers can use to make themselves less dependent on energy providers. Engines from numerous manufacturers will be on show, and these can be operated with biogas, produced from the fermentation of raw materials and by-product residues.
The generated electricity can be consumed locally or fed into the public grid, and at the same time the heat produced can be used for production processes or to warm buildings. It is vital, however, that lean-burn engines are used to minimize the formation of pollutants. Integrated sensors and control systems ensure low emissions by managing the quantity of fuel injected so that the optimum mix of air and fuel is always guaranteed. The gas engines produced by leading international manufacturers all follow this operating principle, as well as being designed for decentralized energy supply in continuous operation when powered by biogas, natural gas or sewage gas.
Stricter limits stimulate new investment
Germany’s air pollution control regulation (known as TA Luft) has recently been amended to introduce stricter controls on engine emissions legislation. As a result, CHP manufacturers attending EnergyDecentral expect an investment boost from plant operators installing new technology. The focus will be on low-emission engines and emission-reduction technologies.
The future specifications for CHP systems with a rated thermal input of between 1,000 kilowatts and 50 megawatts will define limits on carbon monoxide (CO), nitrogen oxides (NOx), formaldehyde (HCHO), hydrocarbons (HC) and ammonia (NH3) emissions. For natural gas engines, for example, the NOx limits will be reduced to 100 milligrams per cubic meter, while the limit will be 500 milligrams per cubic meter for engines running on biogas. No limits are specified for CHP plants with a rated thermal input of less than 1,000 kilowatts, which represent a power output of 400 kilowatts.
CHP plant subsidies
The overwhelming majority of farmers operate installations that will not be subject to the revised TA Luft regulations, but operators of smaller biogas plants will have to manage the formaldehyde emissions from their CHP systems to meet new limits specified in the Renewable Energy Sources Act. From 1 July 2018, a limit of 20 milligrams of formaldehyde per cubic meter will be introduced for biogas plants with outputs of up to 500 kilowatts. Farmers who want to continue receiving the German state subsidy of one cent per kilowatt hour must demonstrate that they are meeting this limit, and in many cases only post-treatment of the exhaust gas will be able to reduce the formaldehyde emissions from existing plants.
This means Selective Catalytic Reduction, or SCR for short, could be an important buzzword at EnergyDecentral. New sulfur-resistant catalyst systems neutralize formaldehyde and, in combination with a retrofittable urea dosing system, nitrogen oxides too. After-market catalyst systems are available that include the urea-dosing system, urea tank and continuous nitric oxide monitoring. A compressed-air-assisted nozzle precisely meters the required amount of urea into the exhaust pipe to reduce the nitrogen oxides in the exhaust gas.
Professional maintenance vital too
As well as innovative technologies, the focus at this year's EnergyDecentral in Hanover will also be on the professional maintenance of existing plants, which is also vital for keeping emissions to a minimum, as well as ensuring trouble-free operation. Most exhibitors at the event offer extensive information and attractive offers related to maintenance and service. In addition, the topic will be reinforced during forum events, with aim of ensuring continuous and long-term compliance with emissions from CHP plants.
March 8, 2018 - EnergyDecentral / EuroTier