Biogas production has been commonplace in other EU countries for years (according to data from the European Biogas Association, EBA). By the end of 2020 there were almost 19,000 biogas plants in the European Union, most of them in Germany, with more than 11,000 plants, followed by Italy (more than 1,600) and France (more than 700), while Spain only had about 300.
One of which is the co-digestion biogas production plant found on the Capdevila Torrent Ramaders Farm located in Alcarràs (Lleida, Spain), run by Josep Capdevila, who we could say was a visionary in our country since, at the end of 2015, he already opted to valorize the manure produced on his 4,000-sow farm and launched the project.
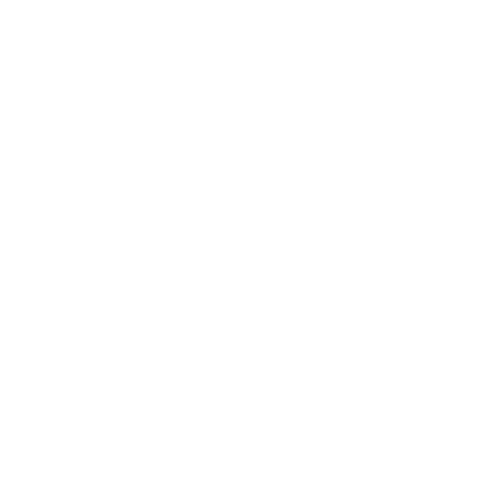
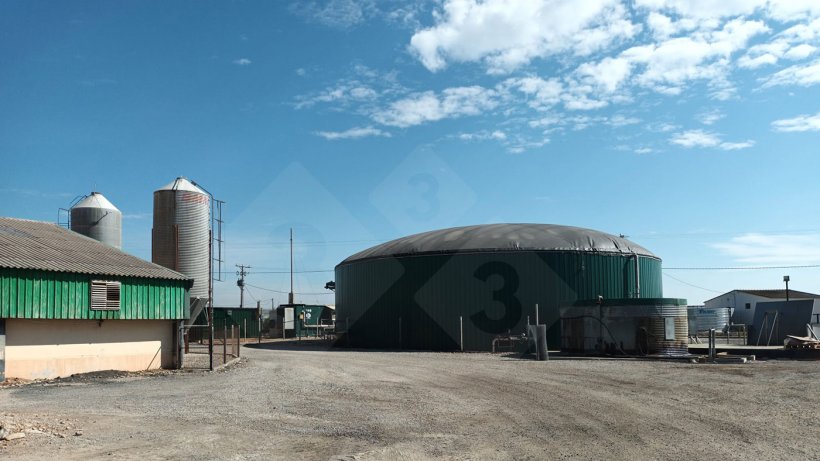
Biogas production plant via co-digestion.
How does a biogas plant work?
The farm produces about 28,000 m3 of slurry per year. The biogas generation plant has a covered reception lagoon with a capacity of 180,000 liters. The slurry is channeled from the barns to the lagoon through pipes. Thanks to a homogenizing agitator with different positions, the fresh slurry is mixed with the co-substrate, in this case, chopped corn grown on the farm's 11 hectares.
Every two days, 800 to 1000 kg of corn silage is mixed with 100 m3 of slurry. The agitator runs for about 10-15 min/day. After mixing, a pump pumps 60 m3 of new material daily to the top of the digester, where the anaerobic process that will produce biogas will take place.
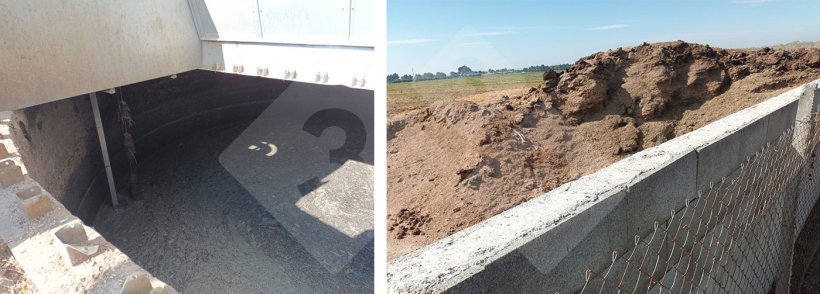
Left: Pre-lagoon mixing of slurry with the co-substrate, in this case corn silage. Right: corn silo.
This digester, 23 m in diameter and 6 m high, has a capacity of 2,400,000 l and has two agitators. It is filled to approximately 5.40 m as a safety measure. There is also an interior safety net so that the tarp never falls in the event of digester failure or when repair work is being done on the digester.
Biogas production remains fairly stable throughout the year since this type of biodigester has an internal heating circuit, which is fed by its own energy production, and which allows the internal temperature to be maintained so that the bacteria can work properly (the optimum temperature in these cases is around 37ºC).
One of the problems with this type of process is the production of hydrogen sulfide, which is highly corrosive. The system has an air compressor that serves two purposes: to insufflate oxygen to help precipitate the hydrogen sulfide and to keep a tube located in the upper perimeter of the digester inflated that acts as a pressurized belt holding the tarp.
On the other hand, we must not forget the digestate, a product with a high fertilizing capacity. It flows down a pipe by gravity and is stored in a lagoon with a capacity of 2 million liters.
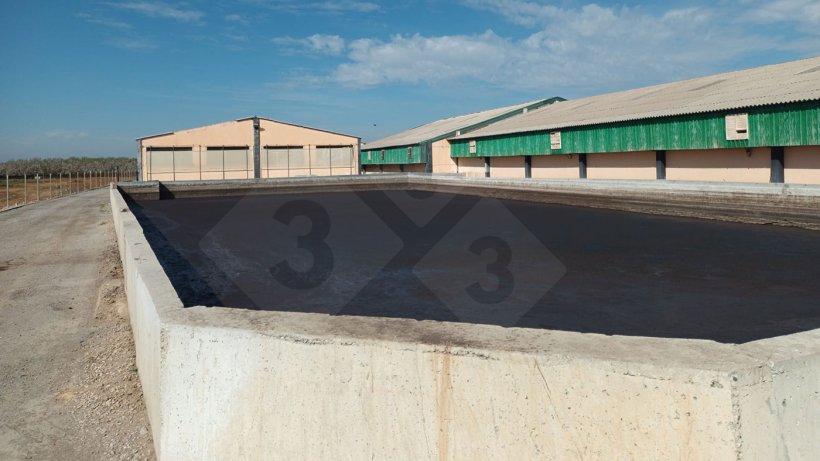
Digestate storage lagoon.
Financial benefits
From the biogas produced, which is 62 to 64% pure, the plant produces electrical and thermal energy. The co-generation engine has already worked 67,000 h and since its start-up, 3,843,000 kW have been produced. The co-digester produces enough gas to supply 100% of the farm's electricity needs, with kW left over to be sent to the power grid. The gas boiler, plus the heat recovered from the co-generator, supplies 80% of the farm's thermal needs (to heat the radiant water circuit in the barns, as well as to maintain the internal temperature of the co-digester), while the remaining 20% of the needs are generated from a biomass boiler.
Last year was the highest production year to date, with a total of 514,000 kW, with engines running an average of about 23.6 h per day (engine maintenance must be taken into account).
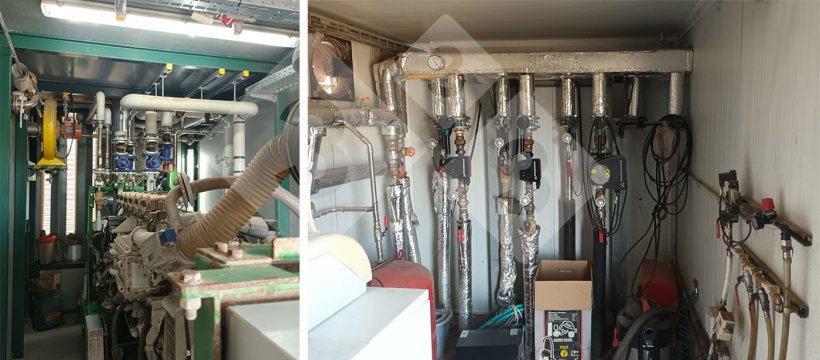
View of the co-generation equipment and boiler and hot water distribution area.
The investment was €480,000 and paid for itself in 6.5 years. Eight years ago, before starting the project, annual electricity and heating costs were around €98,000/year. With current electricity and gas prices, the benefits of biogas production are high.
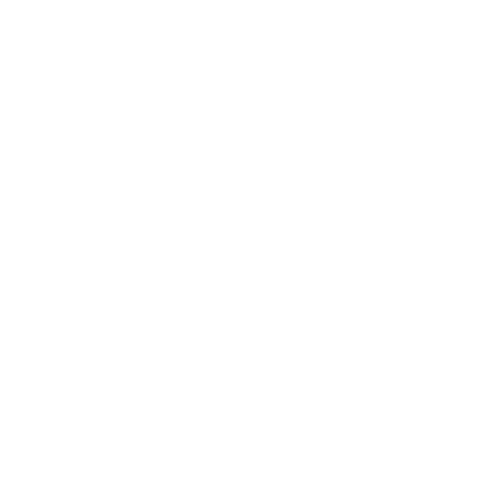
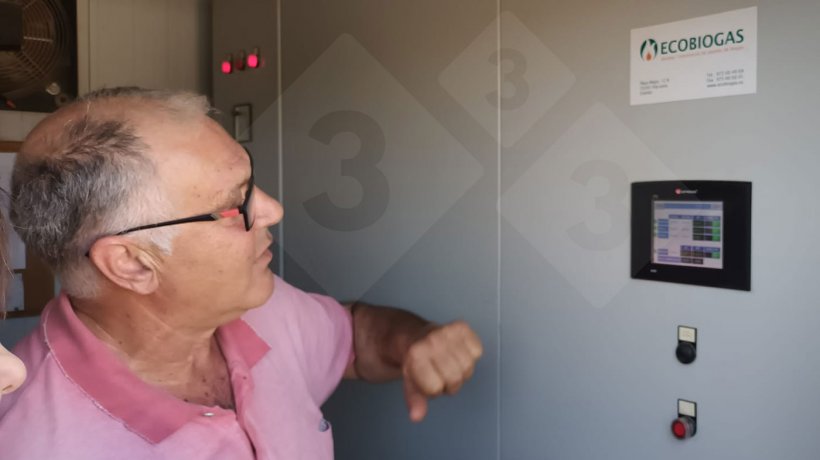
The owner of the farm, Josep Maria Capdevila, controls the setting in the digester.
As for the digestate, in addition to its use on the farm itself, it is sold as fertilizer to different farmers, providing another source of income. The owner says that in recent months, due to the increase in the price of chemical fertilizers, the demand for digestate has increased.
Environmental benefits
Anaerobic digestion of slurry and the consequent production of biogas has a positive environmental impact since it reduces greenhouse gas emissions, produces renewable energy, energy self-sufficiency, stabilized and clean biofertilizer, and reduces odors.