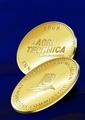
From among the innovations presented, an impartial commission of experts appointed by the DLG and judging on the basis of stringent criteria has selected altogether five innovations for Gold Medals and 28 innovations for Silver Medals.
Gold Medals 2009
*
“CLAAS AUTO FILL”
CLAAS Vertriebsgesellschaft mbH, Harsewinkel, Germany
Hall 13, Stand E02
Chopping is demanding harvesting work. The goal is to achieve optimal filling performance with low stress, risk and field losses. The digital 3-D image analysis from Claas Autofill allows automatic filling of the transport units by day, in mist and by night. Both the ejector manifold and the flap of the chopper are automatically oriented to the trailer contours. The driver no longer needs to concentrate on filling the trailer. This high-level driver-release system substantially enhances the quality of work, efficiency and occupational safety.
*
“Automatic ejector manifold and ejector flap control (tower control)”
New Holland Agriculture Equipment Spa Torino, Italy
Hall 3, Stand C21
Chopping is demanding harvesting work. The goal is to achieve optimal filling performance with low stress, risk and field losses. The 3-D scanner from New Holland allows automatic filling of the transport units by day, in mist and by night. Both the ejector manifold and the flap of the chopper are automatically oriented to the trailer contours. The driver no longer needs to concentrate on filling the trailer. This high-level driver-release system substantially enhances the quality of work, efficiency and occupational safety.
*
“CEMOS”
CLAAS Vertriebsgesellschaft mbH, Harsewinkel, Germany
Hall 13, Stand E02
The electronic machine-optimising service (CEMOS) from Claas is an interactive setting assistance system that contains all settings of all the combine assemblies for different crops and harvesting conditions and guides the driver step by step to the optimal machine setting. Holistic optimising of the combining process is thus made possible for the first time with the aid of a machine-supported setting assistant system. Modern combines are admittedly equipped with programmed setting values in their information system for average harvest conditions. However, when optimising the settings the driver often only alters them slightly to cater to the prevailing harvesting conditions. As a result, most combines harvest with working rates and work qualities that fall short of the technical potential of the machine.The CEMOS system analyses the current situation, devises optimisation steps systematically from the data obtained and suggest these to the driver. The system also takes into account the given basic settings and equipment variants. The driver can accept the suggested setting or request an alternative. If he accepts a suggested setting, he is notified for sensor-monitored settings whether the work result has improved or not. The CEMOS also draws the driver’s attention at an early stage to conflicting targets, such as for example an increase in the broken grain component in the case of intensive threshing out and the technical limits of the selected setting. In a dialogue with the system, it can maximise the work quality and working rate of the combine up to its technical limits. CEMOS is thus a trailblazing milestone in improving efficiency of grain crop harvesting.
* “Cross-manufacturer ISOBUS operating concepts”
Competence Center ISOBUS, Wallenhorst, Germany
Hall 27, Stand G33
(initiated by the firms Amazonen-Werke H. Dreyer GmbH & Co. KG, Grimme Landmaschinenfabrik GmbH & Co. KG, Bernard Krone GmbH Maschinenfabrik, Kuhn Maschinen-Vertrieb GmbH, LEMKEN GmbH & Co. KG und Rauch Landmaschinenfabrik GmbH)
The world’s first cross-manufacturer concept and realisation of user-kindly operating concepts for ISOBUS-compatible agricultural machinery has been implemented in cooperation between several agricultural machinery manufacturers – including market competitors. Identical menu structures, masks for setup and entry, identical pictographs and positionings for intuitive entry and navigation have been developed for both different kinds (e.g. loader wagons, potato harvesters or plough) and same applications with mounted implements from various manufacturers (e.g. fertiliser spreaders). To implement the concept, the companies jointly realised an ISOBUS-Terminal with ergonomic design in accordance with the latest state of the art. In addition to the necessary technical hardware and software interfaces, the focus was placed especially on the human-machine interface. Examples are entry via touchscreen, softkeys and incremental transmitters, single-handed operation or the ISOBUS-Stop-Button. The operating concept realised was tested successfully by interchanging the terminals of various manufacturers and mounted implements and it thus represents a milestone on the way from stand-alone solutions to the necessary introduction of ISOBUS irrespective of the manufacturer in practice.
*
“John Deere ActiveCommand Steering”
John Deere Vertrieb, Bruchsal, Germany
Hall 13, Stand A43
John Deere is for the first time presenting a Steer-by-Wire steering system that intervenes actively in the steering circuit via a controller in order to distinctly improve driving safety and driving comfort. This active intervention in the steering control circuit has not been presented in the car and commercial vehicle sector so far, but instead only formulated as a development goal for the future. The unsatisfactory straight-ahead behaviour that has been evidenced in customary fully hydrostatic steering systems available so far is improved, so that steering activity is reduced and the driver’s workload is distinctly lowered. The steering moment is modulated actively, depending on the driving situation, so that the driver feels a feedback at the steering wheel via his steering manoeuvres. Fast evasive action has so far sometimes led to uncontrollable rocking (oversteering) of the vehicle and this is now actively suppressed with an effect similar to ESP in cars. This effect is felt particularly during fast travel with heavy multiple-axle rigid drawbar trailers. In addition to the safety aspects, the system with a speed-dependent steering ratio additional facilitates operations in the field and front-loading work.
Silver Medals
*
“Automatic knife grinding system for loader wagons”
Alois Pöttinger Maschinenfabrik Ges. m.b.H, Grieskirchen, Austria
Hall 27, Stand D34
Grinding knives on loader wagons has so far been known as time consuming and non-ergonomic work. Pöttinger has succeeded in developing an automatic grinding machine for individual knives in loader wagon cutter units. The automated grinding operation can be carried out several times a day during transport. The complete hydraulic drive is designed simply and maintenance-kindly. Constantly sharp knives with a high cutting quality for efficient performance of work are now possible on loader wagons too.
*
“Front mower EasyCut 32 CV Float”
Bernard Krone GmbH Maschinenfabrik, Spelle, Germany
Hall 27, Stand J15
Pushed headstock with integrated spring weight alleviation and novel spring balancing kinematics for uniform ground pressure under all operating conditions. The EasyCut 32 CV Float is the first front mower with pushed headstock and integrated mower weight alleviation that at the same time allows uniform ground pressure to be maintained through the novel "Float" spring balancing kinematics. Accordingly the advantages of the "pushed" front mower are combined with those of the "trailed" mower without applying any additional load on the front axle as has been necessary so far with other header designs, representing advantages above all on sloping terrain. The extra benefit of the uniform ground pressure is unique.
*
“VariStream”
Bernard Krone GmbH Maschinenfabrik, Spelle, Germany
Hall 27, Stand J15
Variable crop flow system in self-propelled forage harvester for reduced-resistance material flow to cut wear, save energy and relieve the engine. In the Krone VariStream system the front part of the drum base is hinged to the shearbar. When the shearbar is adjusted after grinding of the knives, the drum base in the front area automatically follows. There is thus no "dead space" between the shearbar and drum base that could impair the flow of crop negatively. The rear part of the drum base is mounted on springs and can thus yield under large quantities of feed. At low crop flows, the base returns to the original position thanks to the springs. The risk of clogging is lower, a uniform crop flow is retained and the ejection performance of the chopper drum is not reduced.
*
“Cleanfix Pulstronic - Clean radiator at low cooling fan output"
Hägele GmbH, Schorndorf, Germany
Hall 6, Stand C40
The fan vanes on the Cleanfix Pulstronic can be turned about the longitudinal axis not only to clean the radiator, but also to save drive energy. Depending on cooling requirements the vanes can be positioned in any intermediate position. This allows a control circuit that processes PWM or CAN bus signals of the engine controller and regulates the exact vane position via a position sensor to be integrated in the adjustment mechanism. By contrast with the visco-coupling there is no power consuming coupling slip, regardless of the fan output. In addition the "Flex Tips" fitted at the vane ends are slightly oversized so that they are ground into shape in operation in the front area of the cowl. This effectively avoids air recirculation and additionally enhances efficiency.
*
“Ultra Guidance PSR ISO - ISOBUS-compatible automatic steering"
Reichhardt GmbH Steuerungstechnik, Hungen, Germany
Hall 16, Stand A09
Integration of an automatic steering system – e.g. on the basis of GPS or sensors – typically requires machinery-specific changes (valves, hydraulic hoses) with corresponding expenditure on installation. The steering system is then designed for the specific tractor. The ISOBUS-compatible automatic steering system "Ultra Guidance PSR ISO" now allows a Plug&Go installation of the steering system for vehicles and machinery that are equipped with an ISOBUS interface without the need for hardware adaptation. The information is exchanged between steering system, tractor or mounted implement via ISOBUS. The steering system can thus be operated via any existing ISOBUS terminal of the tractor or mounted implement. It is independent of the tractor, so that users can select steering systems and vehicles independently of the manufacturer to match their own on-farm requirements and deploy them universally.
*
“GEOseed”
Kverneland Group Deutschland GmbH, Soest, Germany
Hall 5, Stand E38
The new system allows uniform, large-scale planting of beets or maize in triangular or rectangular patterns. It is to be expected that labour management and environmental friendliness can be improved by simplified and more efficient deployment of mechanical weed control (cross-hoeing). Furthermore, more effective utilisation of growth resources such as space and nutrients is to be expected.
*
"smartControl – automatic stripping regulation in the EDX precision drill“
Amazonen-Werke H. Dreyer GmbH & Co. Hasbergen, Germany
Hall 14, Stand A20
For the first time automatic and adaptive control of the stripper position ensures the isolating quality of a precision drill. This substantially improves the quality of work in maize drilling, especially at high speeds of travel.
*
“Intelligent Loader Wagon Combination”
Alois Pöttinger Maschinenfabrik Ges. m.b.H., Grieskirchen, Austria
Hall 27, Stand D34 and
John Deere Vertrieb, Bruchsal, Germany
Hall 13, Stand A43
Pöttinger uses the new opportunities offered with the "intelligent loader wagon" that if necessary not only stops the tractor, but also steers the speed of travel of the combination depending on the windrow density. The windrow form is determined with ultrasonic sensors mounted at the front of the tractor. As the data are collected ahead, the tractor has sufficient time to respond and adapt its speed. The system not only has a target value for speed, but also controls acceleration. It operates in combination with a sophisticated sensor system on the loader wagon at all relevant speeds of travel and improves the efficiency of the overall process, at the same time distinctly relieving the burden on the operator.
*
“John Deere Tractor-Implement Automation”
John Deere Vertrieb, Bruchsal , Germany
Hall 13, Stand A43
On the basis of an extended ISOBUS protocol, John Deere enables certified implements to access safety-relevant tractor parameters (e.g. speed/strategy of travel, hydraulics, pto shaft). John Deere demonstrates this option with the example of a round baler in order to enhance its performance capability and relieve the workload of the driver. After the bale chamber is filled, the tractor stops automatically; following the wrapping operation the tail flap is opened and closed by the baler activating the hydraulic control valves of the tractor. This not only makes it possible to automate the entire procedure, but also does away with the need for the hitherto necessary double equipment with electro-hydraulic control units on the baler.
*
“Automatic fan speed setting in sloping terrain”
New Holland Agriculture Equipment Spa, Torino, Italy
Hall 3, Stand C21
Customary slope compensation systems for combine cleaning only react to lateral inclination. If a combine harvests in the rise and fall line, during uphill work this can lead to blowing over of grain and non-grain constituents from the cleaning unit and hence to elevated grain losses. During downhill travel the layer thickness on the screens increases and higher quantities of non-grain constituents enter the grain tank; if the layer thickness is too high this also leads to higher grain losses. The speed control of the New Holland cleaning blower independently of the slope gradient is the first to adjust the blower speed automatically to the respective combine inclination in uphill and downhill work depending on the crop. This allows uniform work quality and work output during harvesting on sloping fields without the driver having to intervene, thus facilitating work, and is a trail-blazing detail improvement in grain crop harvesting.
*
“HR lifting unit for the beet lifters Terra Dos T3 & Terra Dos T3 Plus”
Holmer Maschinenbau GmbH, Schierling-Eggmühl, Germany
Hall 2, Stand A48
The individually suspended HR lifting unit makes it possible for the first time to orient the lifting depth to each individual row in the case of multi-row lifting work. Ground unevenness in the sugar beet seed bed, ruts or erosion have so far necessitated a lifting depth oriented to the deepest beets within the working width of the lifter, with the known disadvantages. This development allows energy saving and at the same time gentle harvesting with low earth adhesions.
*
"iTANK" filling level and flow rate measuring system”
Josef Kotte Landtechnik GmbH & Co. KG, Rieste, Germany
Hall 15, Stand A11
The relatively low-price iTank system from Kotte measures both the filling level in liquid manure tankers and the flow rate. These measurements make it possible to switch off automatically during filling operations. Alternatively, the spreading rate per hectare and a range can be calculated and displayed during field work.
*
“LED individual nozzle lighting”
Amazonen-Werke H. Dreyer GmbH & Co.KG, Hasbergen, Germany
Hall 14, Stand 20
*
“HD-Nightlux”
Herbert Dammann GmbH Pflanzenschutztechnik, Buxtehude-Hedendorf, Germany
Hall 15, Stand C12
Both manufacturers use the high light intensity of LEDs to make the spray compartments of the nozzles on the sprayer boom easily visible during evening and night time hours. Nozzles that do not function soundly and create incomplete or no spray patterns can be identified in this way – in as far as they are visible during spraying – and can thus be cleaned or exchanged. A further advantage lies in the fact that the plant stand to be treated is visible to the driver even beyond the working width of the equipment so that he can react to obstacles in good time.
*
“Expanded i-solutions for John Deere plant protection sprayers”
John Deere Vertrieb, Bruchsal ,Germany
Hall 13, Stand A43
John Deere is expanding its trailed implements of series 700i and 800i to include functions aimed at precise tank filling, more precise spraying of the residual quantities remaining in the equipment, and improved cleaning and spreading of the residual liquids. The central operating terminal is the GreenStar 2600 for setting, monitoring and executing known functions. The new integrated Tank Fill Calculator calculates the necessary quantity of water and pesticides necessary for the specific tank filling (even if it is not yet completely emptied or for remaining residual areas). The necessary water and agent quantities are printed out on a sheet. With the aid of GPS controlled application, the remaining area still to be treated can be determined exactly and the quantities of water and pesticide required for this are ascertained. If these quantities are dosed exactly, residual quantities can be reduced to a minimum. The Auto Dilute System takes over subsequent cleaning of the sprayer equipment that is executed automatically, regardless of whether cleaning and spraying are to be carried out in accordance with pre-selected dilution factors (1:6 or 1:100) or in a continuous operation. The system offers the following advantages:
- Distinct relief of the burden on the user by reducing the risk of operating faults*
- Reduction of remaining residual quantities and environmental pollution
- Avoidance of wrong dosing, improved documentation
- Facilitated mixing of the desired spray fluid
- Continuous customer benefits thanks to faster, exact filling, cleaning and spraying
“LEMKEN VariExtend infinitely variable sprayer boom”
Lemken GmbH & Co. KG, Alpen, Germany
Halle 11, Stand B45
The sprayer boom is built up in segments and the boom width can be varied in the working position by extending or retracting the segments. A asymmetrical boom width is also possible. Here the outer segments of the spray boom remain in their outer position so that the functionality of collision protection in the pushed area is maintained in full. The boom can easily be adapted to different working widths or tramline spacing. Consequently any obstacles on the fields can be cut out exactly without having to veer from the track.
*
“LEMKENConnect”
Lemken GmbH & Co. KG, Alpen, Germany
Hall 11, Stand B45
The "QuickConnect" system substantially facilitates three-point hitching of implements. Connecting of top links, articulated shafts, hoses etc. can be carried out with sufficient space between tractor and mounted implement. After the tractor reverses, the quick connect couplings engage in the bottom link bolt and the top link is automatically guided to and stopped in its end position by the unit. This second part of the coupling operation can be carried out without any need to alight from the cab. Additionally the coupling system brings the mounted implement closer to the tractor. This new coupling system offers the following advantages:
- Coupling can be carried out comfortably and safely by a single person.*
- Increase in working and transport safety through shifting of the centre of gravity of the mounted implement towards the tractor.
"Ultralight 800“
Biso Schrattenecker GmbH, Ort im Innkreis, Austria
Hall 5, Stand D06
Large combines with wide cutterbars achieve the highest hectare performance. For this reason headers are continually wider and thus heavier. Additionally, adjustment of attachments on wide cutterbars has often to be carried out on both drive sides. The Ultralight 800 12 m cutterbar from BISO-Schrattenecker is uniquely constructed of hollow aluminium elements (patent pending). These load-bearing elements are screwed into one another in a module system and form not only the basis for differing working widths but also a lightweight carrying frame for the other working parts. All adjustments for meeting the differing harvest conditions are carried out either electro-hydraulically or via central spindles. The cutterbar which can be extended to cover a wider working width is, with its lightweight construction, a future-oriented further-development.
*
“Intelligent database for plant protection agents with integrated active suggestions on the basis of the plant cultivation software AGRO-NET”
CLAAS Agrosystems GmbH & Co. KG, Gütersloh, Germany
Hall 16, Stand A11
Integrating the Proplant database with current day-to-day information about all licensed plant protection agents into the Agro-Net plot file greatly facilitates plant protection operations for farm managers. By coupling with the web-based database, the user is not only on the safe side as regards licensed products, but is also actively supported in selection of agents. In combination with the plot file information on plant stands, the field and its history are compared with the indication list of the plant protective agent database and agents are proposed in line with requirements laid down under licensing law. The innovation not only promotes safety, but is also expected to save time for stand management.
*
“Smart-Braking-System”
New Holland Agriculture Equipment Spa, Torino, Italy
Hall 3, Stand C21
New Holland's ABS system offers not only the generally known safety benefits, but also caters to the specific demands of agriculture. For instance it allows the popular individual wheel braking and correspondingly small turning radius during headland operations for the first time. The inner wheel in the bend is delayed specifically in proportion to the steering angle without causing any blockage with damage to the track. The system also serves as a starting aid on hillsides, is gentle on the soil and relieves the burden on the driver.
*
“Tyre pressure regulating system for Fendt 900 Vario”
AGCO GmbH, Marktoberdorf, Germany
Hall 9, Stand E18
Fendt satisfies the calls by practical farmers for an integrated tyre pressure regulating system as standard equipment covered by the warranty conditions for the overall vehicle on standard tractors for the first time. Adaptation of the tyre air pressure in line with needs means greater safety, less tyre abrasion on the road and more gentle treatment of the soil in conjunction with higher traction efficiency on the field. The system is operated comfortably via the Vario terminal, and in addition to a safety structure also provides the option of setting the trailer tyre pressure via the ISO-bus.
*
“EasyGuide Center Link from John Deere”
John Deere Vetrieb, Bruchsal, Germany
Hall 13, Stand A43
In today's customary, heavy-duty hydraulic top links, mounting equipment and implements becomes a feat of strength that takes many operators to the limits of their powers and thus involves scope for injuries. This is definitely the case with mounted implements that only allow restricted movement space during the coupling operation. John Deere solves this problem by using a relieving spring that carries the top link along with it and so makes it possible to connect with the aid of a rope from the safety of the cab. The top link is stabilised sideways too with the aid of a centering spring.
*
“Fliegl »Toplift« lifting cover”
Fliegl Agrartechnik GmbH, Töging, Germany
Hall 25, Stand A12
Cargo in high cone-shaped heaps can also be covered quickly and safely using the hydraulically actuated cover hood. This prevents the air stream generated from blowing away the harvest and foods are protected against bird droppings and rain. This not only means greater safety for other road users, but also does away with the need for manual covering at a height of up to 4 m and so improves user safety.
* “Bandit roller belt wagon”
Krampe Fahrzeugbau GmbH, Coesfeld, Germany
Hall 25, Stand C12
Loading and unloading of this body trailer are carried out via a fabric belt that is wound up alternately by hydromotors mounted one at the front and one at the rear end of the cargo platform, thus moving the cargo. The advantage of this design over a push-off wagon is the higher payload and lower hydraulic power requirement. Delicate goods like potatoes can be unloaded gently, and pallets and general cargo can be set against the tail flap and carried forward for loading.
*
“Soil Load Monitor (SLM)”
GRASDORF WENNEKAMP GmbH, Holle, Germany
Hall 12, Stand C13
An ultrasonic sensor in the wheel rim continuously measures the tyre deflection and thus provides a characteristic according to which the minimal tyre pressure can be set as a function of load and speed. Consequently the maximum contact area can be achieved in every situation (= soil conservation). The temperature-compensated measurement is transmitted in wireless fashion from the rotating wheel into the cab. The minimum admissible tyre pressure can thus be safely set and overloading of the tyre with consequences for service life and safety can be ruled out.
*
“Condition Monitoring System for John Deere forage harvesters”
John Deere Vertrieb, Bruchsal, Germany
Hall 13, Stand A43
As working rates of harvesting machinery increase, avoiding repair-related downtimes becomes ever more important and makes a crucial contribution to lowering costs and improving operational reliability. Installing acceleration sensors at critical bearings on a forage harvester makes it possible to identify failures at an early stage on mobile machines for the first time. Preventive repair can not only avoid downtime during work with subsequent stoppage of the entire ensiling chain, but also prevent the consequential damage frequently connected with bearing damage. The monitoring system is integrated in the JDLink telematic system that in addition to documenting faults also offers the option of alerting users via the GSM network.
*
"Belarus 3023“
Traktorenwerk Minsk, Minsk, Belarus
Hall 5, Stand D35a
The 220 kW standard tractor has a diesel-electric drive with modern control electronics and good efficiency levels. The front pto is powered electrically and its rpm speed is thus largely independent of the internal combustion engine. Up to 172 kW electric power can be passed on from the internal DC high voltage network to external users that display corresponding power requirements.
*
“STIHL MS 441 C-M”
STIHL Vertriebszentrale AG & Co. KG, Dieburg, Germany
Hall 26, Stand K21
The STIHL MS C-M power saw is the first professional power saw equipped with standard installed fully electronically regulated Motor-Management (M-Tronic). The M-Tronic improves starting behaviour and optimises motor running in a wide variety of operating conditions, thus ensuring higher operational reliability and user kindliness.
http://www.agritechnica.com/90.html?wb2218=aHR0cDovL3ByZXNzZS5kbGcub3JnOjgwODEvL3B1YmxpY0FydGlrZWxEZXRhaWwuZG8%2Fc3ViPWFncml0ZWNobmljYTIwMDkmYXJ0aWtlbElkPTI2OTEma2F0ZWdvcmllSWQ9MTAmc3ByYWNoZUlkPTImYmVyZWljaD1OZXdz